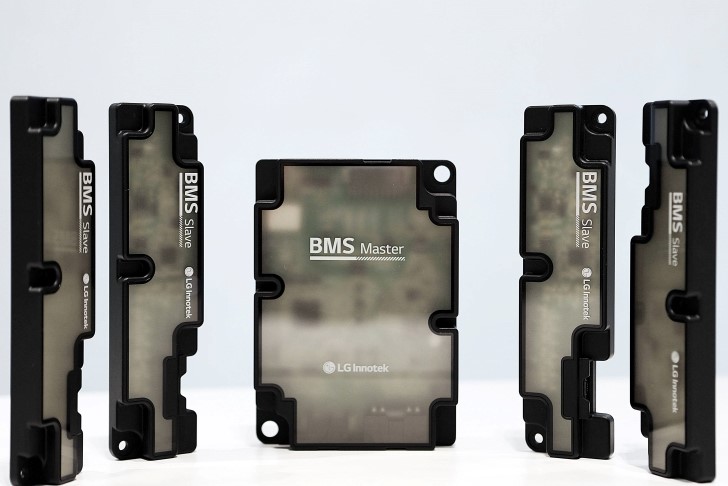
The wireless BMS that LG Innotek developed is embedded with an Radio Frequency (RF) communication module that combines essential components for wireless communication, such as a RF communication chip and antenna, into one unit for the first time in the world. With this product, the company is regarded as having proven its competitiveness to occupy the rapidly growing wireless BMS market in advance.
The key advantage of a wireless BMS is that it contributes to reducing the weight of vehicles mounted with a BMS. Once the cables connected to the BMS are removed, the vehicle weight is reduced by 66~198Ib. Removing the dozens of cables and connectors required for a BMS reduces both the weight and volume of a battery pack.
This secures additional space of 10~15% for a battery pack, enabling increasing the capacity of a battery. That is, the mileage of an electric vehicle can be increased further. It has been confirmed that a wireless BMS increases the mileage of an electric vehicle by up to 12mile. The additional space for a battery pack improves the flexibility of battery design and allows, for example, changing the battery pack structure, increasing the added value of this item.
In addition, the adoption of a wireless BMS enhances the reliability of a product that uses it still further. This is because the possibility of a cable or connector failure due to vehicle vibration is completely removed. Furthermore, the assembly of a battery pack previously conducted manually due to the complexity of cable connections can now be automated using a robot, achieving cost reduction.
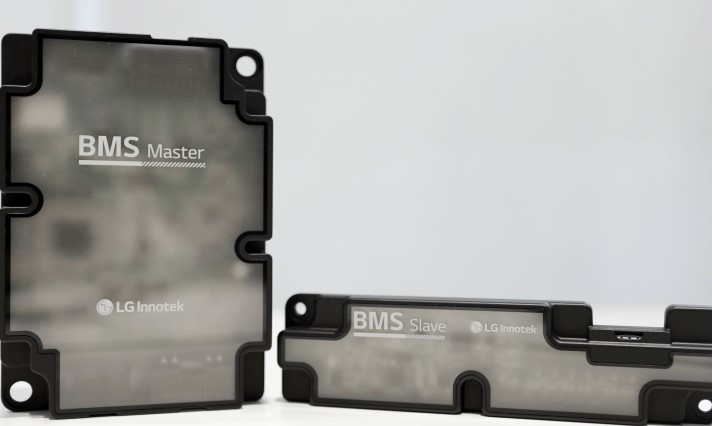
The company’s new product employs 800V, which is the highest voltage among commercially marketed BMS’s. The company had already succeeded in developing an 800V wired BMS in 2020. Since the charging duration decreases as the voltage increases, domestic and overseas automobile makers tend to adopt 800V as their voltage system for electric vehicles.
To send and receive data for an electric vehicle battery wirelessly, a wireless BMS must be equipped with dozens of components such as an RF circuit, RF communication chip and antenna.
In the case of previously released wireless BMS’s, these components were attached one by one to a PCB. Because of this, the BMS production process required a lot of time and there was too much development burden in expanding the product lineup.
On the contrary, LG Innotek first applied to its wireless item an RF communication module that it had developed using its high-precision, high-density, multi-layer board technology. The RF communication module is composed of a four-layer board and dozens of wireless communication components that were densely integrated into this board. This structure helped the company to develop a wireless BMS on which the battery pack could be mounted much more easily.
Above all, the RF communication module mounted on the company’s wireless BMS is designed to be compatible with all types of communication chips. This compatibility enables applying the company’s Wireless BMS easily to all electric vehicles produced by its clients.
LG Innotek established a simulation technology for the first time in the industry that enables virtual inspection of wireless communication quality on its own at the development stage of a battery pack.
The company’s virtual inspection system has proven its effectiveness by showing that the communication quality of wireless BMS’s that it had predicted matched the actual measurement results by more than 95%. The company’s virtual inspection system ensures only products that passed the inspection to be provided to its clients and thus eliminates the need for automobile and automotive component manufacturers to request a separate inspection test.