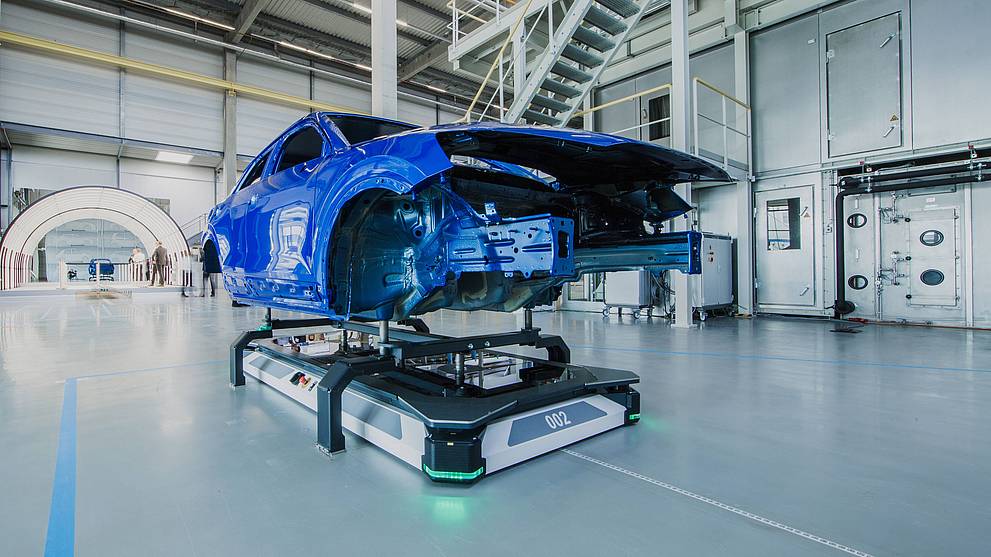
AGVs are key to a smooth transition between work decks and temporary factory storage, covering most of the painting process spectrum. EcoProFleet is designed for this variety. The AGV can pick up any model, from compact cars to SUVs and pick-up trucks to unique shapes like truck cabs, place them down in work decks, or keep them ready during the painting process.
In the paint shops of the future, where modular work boxes replace the old lines with their rigid cycle times, AGVs are on the move up to 24 hours at a time, in the case of the EcoProFleet. It is the only driverless transport system on the market now that can operate around the clock since it does not need to charge its energy stores overnight like other models. Instead, EcoProFleet connects briefly to charging points along its routes. These charging points are where the AGV would be stationary anyway, for example, when transferring a body to a work deck. The short interval is enough to charge the capacitors so that the AGV has enough energy after placing down the body to return immediately to the production area and start the next job.
DXQlogistics.control is Dürr’s tailored software solution for the driverless transport system’s control logic. It controls the material flow digitally according to work deck utilization, equipment and availability.
The software can decide autonomously about the next job step and work deck based on the body type and defined process steps. To optimize logistics, it can also take in destinations outside the route chart, such as outward transfer stations or temporary storage locations. This means it can always respond flexibly, for example, if a malfunction occurs at a work deck or rework to a body surface necessitates changing the original route.
Ultimately, the combination of the EcoProFleet driverless transport system and the DXQlogistics.control software solution results in the optimal utilization of all work decks. Workers no longer need to wait for the next body since the software plans all the tasks ahead and even factors in transport time. Unproductive downtimes and cycle time losses thus become obsolete, replaced by production efficiency.