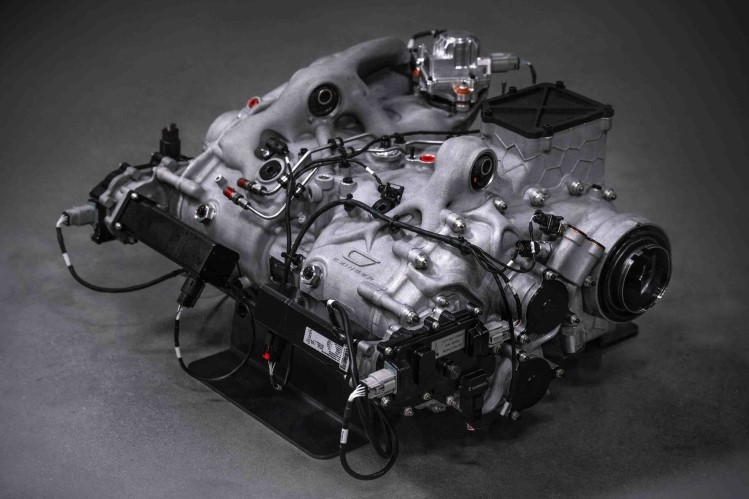
Czinger Vehicles has introduced yet another world-first innovation, partnering with the global leader in Motorsport & High Performance Automotive (HPA) gearbox production, Xtrac, to pioneer the first topology-optimized and additively manufactured gearbox case. The production of the gearbox uses a unique printing process and proprietary aluminum alloy, resulting in significant mass savings, outstanding structural performance, production quality, and efficient printing times. Furthermore, this approach eliminates the need for tooling, achieving a substantial reduction in development time, and the ability to make real-time design improvements. The gearbox is an early example of the company applying this advanced technology to powertrain systems and further enables the 21C’s industry leading performance.
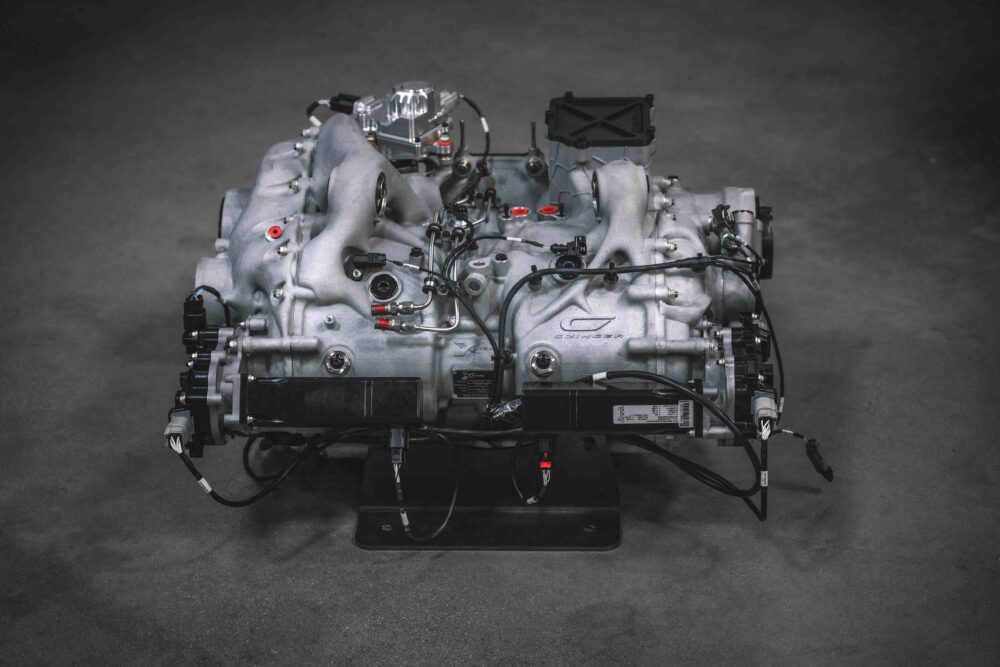
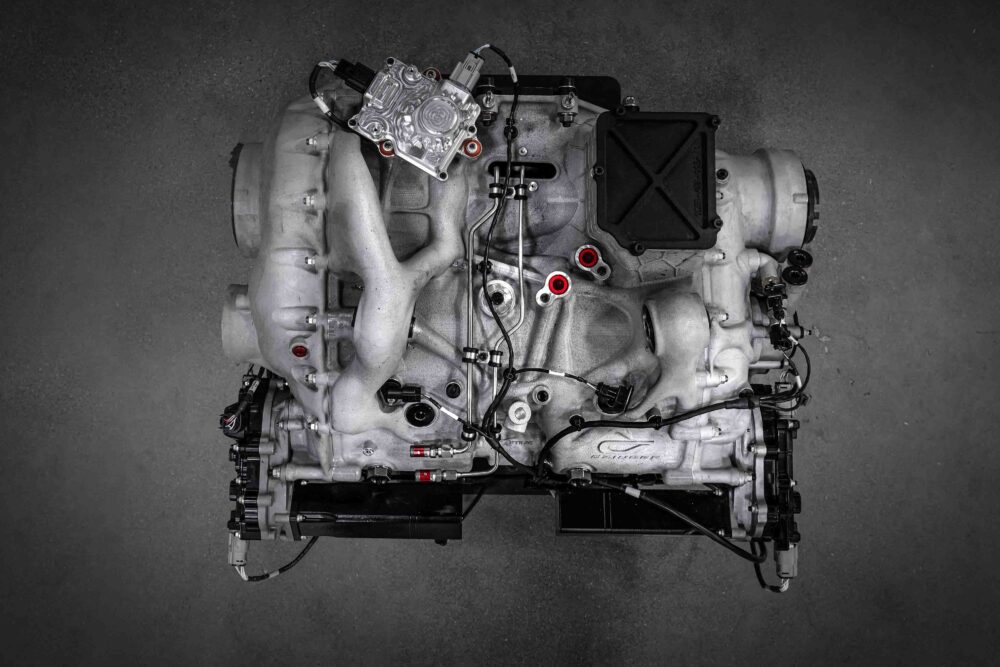
The cutting-edge gearbox boasts leading performance specifications:
- Automated 7- speed semi-sequential gearbox.
- First 48V-electrically actuated twin barrel system resulting in the fastest automated single clutch synchromesh gearbox in existence.
- Dual barrel gear actuation allows for seamless EV-to-Rear Drive blending for smooth city driving.
- Sub-100ms shifts combined with blending of front-axle EV power allows for seamless shifts for high performance driving.
- Highest torque transmitted per mass of gearcase for any road-legal vehicle.
The last time I cared to even bother to look at the print times of the machines that can make these…
it was about 24hrs for a single part; not great, let alone subsequent annealing in a whole other machine.
so you buy a 4MillionUSD 4-laser machine that can print anything you want… it makes about 1 part, per day.
dare i ask if the material cost of the powder is on parity with bulk cast parts?
spend another 1MillionUSD on secondary-process machines to mill and lathe features into it for bearings et al
all to be ‘first’ in some genre that is meaningless to mass-production.
but kudos in being the most efficient in prototyping a handful of parts per year.