More and more electric cars can access fresh energy at fast-charging stations. With a charging capacity of several hundred kilowatts, such a station can replenish a battery to 80 percent within a half hour, for example. The amount of energy flowing into the battery is two or three times higher than when the direction is reversed and energy is released, even under high-performance conditions. As a result, the battery heats up considerably during this supercharging. This can have a negative impact on its power consumption and service life, among other things, if the cooling system is not up to par. Conventional liquid cooling systems that chill entire battery cell systems from the outside are pushed to their limits. That is why automotive manufacturers are increasingly focusing their development on an innovative liquid cooling system that embeds the cells and their electrical arresters in the cooling medium (battery immersion cooling): The medium flows directly around the individual cells and effectively dissipates the released heat.
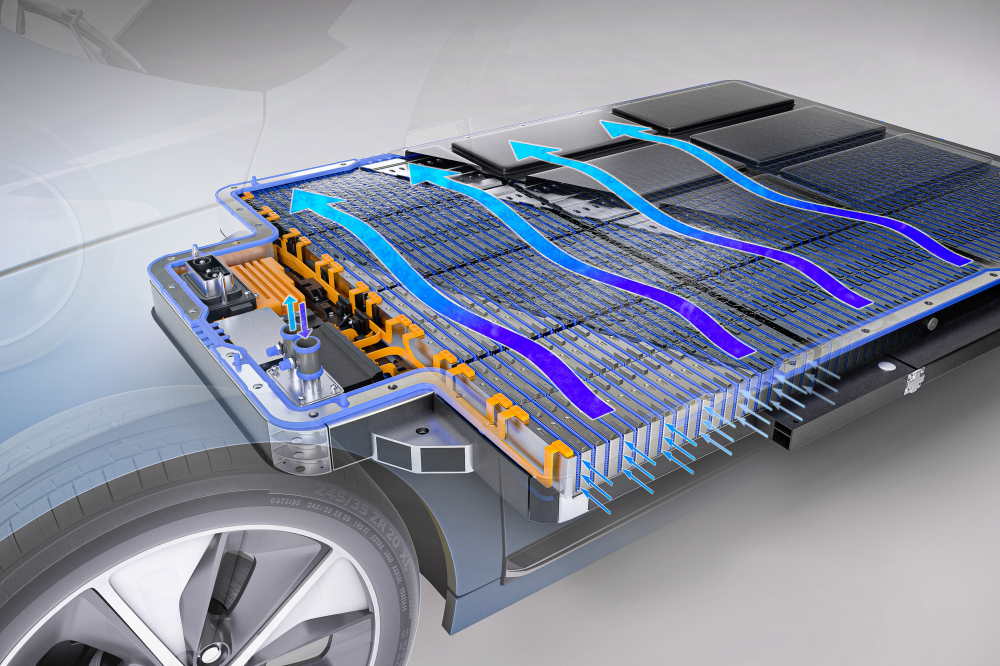
The cooling media used in these kinds of systems have different chemical properties than those in other prevalent media to date. Their direct cell contact, for example, requires electrical insulation. Vehicle manufacturers are examining several partially innovative substance classes of cooling media with vastly different chemical properties.
As essential components for such cooling systems, sealing elements must have chemical properties suitable for the cooling media. This is also true for components such as fasteners, cell spacers and media storage units. For this reason, and to obtain a broad database for specific customer inquiries, the experts in the Material Predevelopment department at Freudenberg Sealing Technologies performed a comprehensive study to analyze the suitability of polymer materials for media used in immersion cooling systems.
The materials relevant to the company were exposed to various fluids. The tests included isoparaffinic oils and ester-based oils, for example, which are specified and widely used for direct battery cooling. In addition to the most conventional fluids, the materials experts also examined the types currently being worked on by the development departments of fluid manufacturers.
Standardized test specimens consisting of the polymer materials were immersed in the fluids for a defined period. To take long-term effects into account and speed up the immersion, the temperature was much higher than is usual and desired for battery systems. The experts then determined the physical key properties of the test specimens that are crucial for the full functionality of a seal over its entire service life, such as volume, weight, recovery behavior, elongation at break and hardness.