JFE Steel and thyssenkrupp Steel Europe have jointly launched a new 980 and 1180MPa class high-strength steel for cold forming.
The products, which achieve higher yield strength and ductility, especially excellent local ductility, compared to conventional high-tensile steel sheets, will contribute to lighter-weight automobile body frames (body in white) and better crash safety performance. The new sheets also are expected to help raise productivity and lower manufacture costs by enabling customers to produce complicated-shape components using conventional cold forming (press/roll) rather than hot stamping.
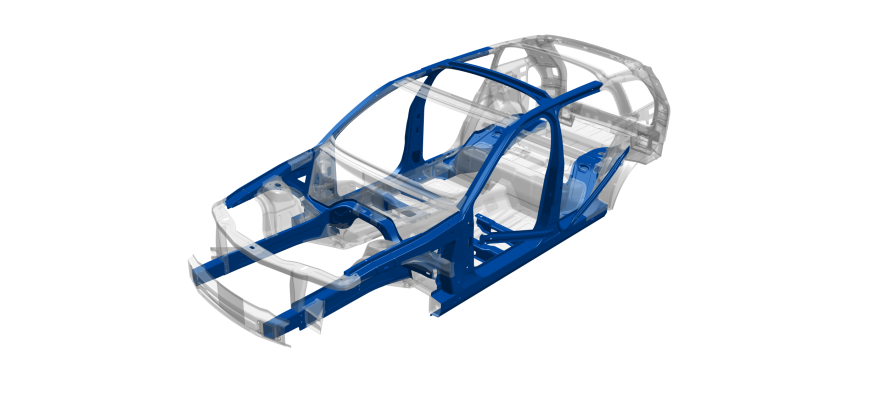
Front Side Member
Rear Side Member
Rocker/Side-sill Outer
Seat Cross Member
A Pillar Applications
B Pillar Applications
Demands are growing for automotive designs that achieve energy savings, weight reduction for reduced CO2 emissions and enhanced crash safety performance. Steel that offers high strength for weight reduction, however, inevitably suffers from inferior formability, which is why it has been difficult to use high-strength steel to produce automotive components in complicated shapes.
To overcome this challenge, JFE and thyssenkrupp Steel have developed these products by designing a new steel composition & microstructure especially focusing on the local ductility of steel and by establishing a new heat treatment method utilizing the Quenching & Partitioning process (A metallurgical process that stabilizes at room temperature by quenching and reheating the austenite phase, which is produced at high temperatures and contributes to ductility.).
The products will be supplied globally by JFE and tkSE for a wide range of applications in next-generation automobiles, including electric vehicles. The sheets will come in strength levels of 980 and 1180MPa and offer various types of coatings, including uncoated, galvannealed and galvanized.